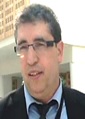
Abdelkhalak EL HAMI
Normandie Université, France
Title: Reliability end optimization of embedded mechatronic systems: What applications for the automotive and aeronautics industry
Biography
Biography: Abdelkhalak EL HAMI
Abstract
Reliability-Based Design Optimization (RBDO) in embedded electronics and mechatronical system is a very important part in several industrial fields. The RBDO analysis of industrial systems is a very important engineering issue, in order to guarantee their functional behavior. Most of the critical failures are generated by the interactions between the sub-systems, implemented in different technologies, e.g. mechanics, electronics, and software. Therefore the analysis of the system as a whole is not enough and it is necessary to study all the interactions in order to estimate the system reliability.
In the embedded electronics and mechatronical system design, it is very important to minimize the structural cost and to maximize safety. Few designers (or researchers) can work with these two opposite philosophies. The basic idea is to know the role of each parameter in our design using advanced technologies in CAD (Computer-Aided Design) domain such as sensitivity analysis, optimization concept and reliability analysis. Our main challenge is to integrate the reliability analysis in the optimization procedure that allows us to define the best compromise between cost and safety. This model is called Reliability-Based Optimization. We applied reliability-based optimization on the three structural optimization families.
Model 1: The Reliability-Based Design Optimization (RBDO) consists of the integration of reliability analysis into the optimization procedure. The classical RBDO approach is carried out in two spaces: normalized space and physical one. Therefore, the nested problems necessitate a high computational time. In order to overcome this problem, we propose a new hybrid formulation consisting in solving the problem in a Hybrid Design Space (HDS), containing all numerical information about the optimization process. Application of Dynamical and fatigue of structures.
Model 2: The Reliability-Based Shape Optimization (RBSO) consists of the coupling between several models: geometrical modeling, numerical simulation, and reliability analysis and optimization methods. The hybrid method can be used efficiently to reduce the computational time. Since the structural geometry may be updated during the optimization process, a flexible model has to be used. After having studied different ways of geometrical modeling, we select a parametric boundary description such as B-spline curves. Furthermore, the design model may be different than the mechanical one and may then give inaccurate results of the structure behavior. We study the relationship between CAD and FEA (Finite Element Analysis) models in order to define the suitable method that updates the geometry with a small cost. Furthermore, the optimization process generally needs gradient evaluations at each iteration. Two problems can be found: the computing time and the result accuracy. Therefore, we propose a new numerical derivative to balance the computing time and the precision. Application of dynamical and noise of structures.
Model 3: The Reliability-Based Topology Optimization (RBTO) is based on the introduction of the reliability criteria into the topology optimization procedure. The resulting reliability-based topologies are different than the resulting deterministic one. Moreover, the advantage of RBTO is to provide the designer with several solutions in function of the target reliability
During this talk, I will present the last developments of Reliability-based Design
Optimization in embedded electronics and mechatronical system.